Top solutions for your manufacturing frontline challenges
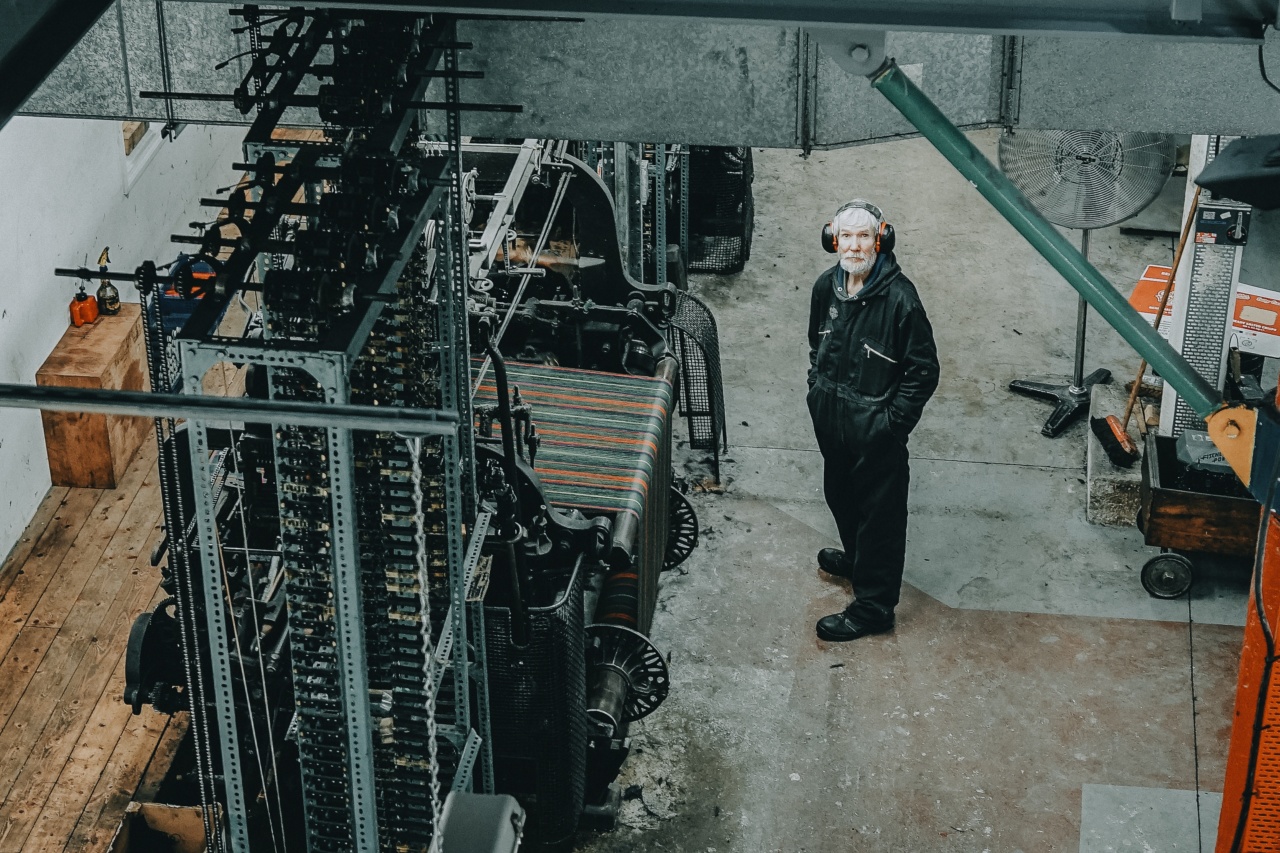
Manufacturing frontline employees are some of the hardest workers in the industry. Is your organization limiting their potential for success?
In most U.S. states, the Manufacturing Industry is one of the most significant sectors of the economy. These jobs entail the creation of new products from either raw materials or components and are found in factories, plants, or mills.
There are around 12.75 million Americans in manufacturing jobs, according to the National Association of Manufacturers reported from the Bureau of Labor Statistics, many of them in the Midwest and California.
The Unified Frontline – An intranet guide to improving frontline worker performance
These states have high concentrations of manufacturing employees in industries such as fabricated metal products, food, machinery, and transportation equipment manufacturing. (U.S. Census Bureau)
While manufacturing output continues to rise, the total number of manufacturing jobs in the U.S. has decreased in the past three decades. This decline can be credited to their inability to meet not only the demands of their industry but also the demands of their frontline workforce.
Four of every five Americans (81%) know that the total number of manufacturing jobs in the U.S. has decreased over the past three decades.
Pew Research Center
Sources place manufacturing employees as some of the most productive in the world, yet, job losses have been highly visible. 89% of manufacturers are leaving jobs unfilled. This loss of qualified applicants could leave millions of vacant positions between 2018 and 2028 — costing the industry $2.5 trillion by 2028. (Deloitte)
To experience a revival in the manufacturing sector, they must first address some of their major frontline challenges:
Recruitment and retention:
The importance of recruiting spans across each and every industry and Manufacturing is no different. In fact, given the specificity of many manufacturing positions, finding and keeping employees that possess the necessary skill sets and abilities is increasingly tricky.
The conditions that these employees are subject to (poor culture, isolation, and more) do not help the process. Stagnant recruiting budgets and a lack of investment in frontline employees only further emphasize the issue.
Manufacturers expect 2.69 million jobs to be vacated by retirees with another 1.96 million opening up due to industry growth. If turnover rates continue to be an issue, finding and keeping frontline manufacturing talent over the coming years will be more difficult than ever.
High turnover rates, low engagement, and decreased productivity are easily blamed on employees, but the genuine blame lies with the organization.
The survey, Understanding the Impact of Quality Candidates, found that nearly half of workers (45%) say that salary is the biggest reason that employees change jobs, followed by a desire for career advancement opportunities (32%), and then better benefits at 29%.
Frontline Solution
The solution begins at the recruiting process. Bringing aboard new talent is easy, making sure they stick is the hard part. Find out not only if they fit your values but also what they are looking for within your organization. Ensuring an accurate cultural fit confirms that your employees understand the company mission and
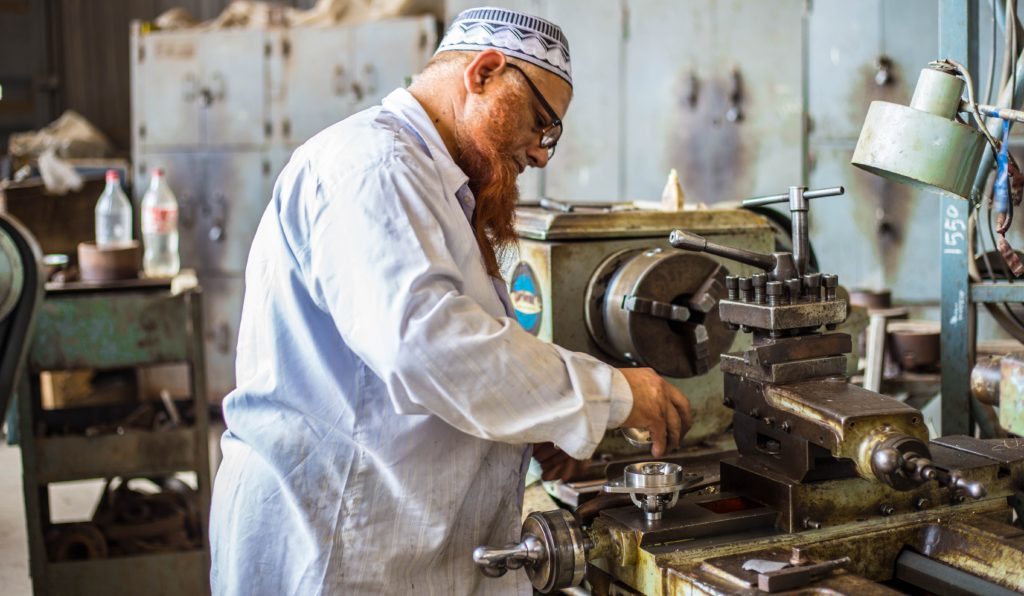
Next step is to make it clear that frontline satisfaction and growth is crucial. Let them know what to expect from the role and in turn, listen to their needs and requests. A space for two-way communication and the right benefits can be the leverage you need to boost EX and frontline retention.
Engagement:
At an estimated 25% employee engagement level, the manufacturing sector trails the national average by 8%. In the face of an outwardly declining workforce, this industry continues to do a poor job of engaging their frontline employees.
These organizations are experiencing a significant rise in global competition, and the risk of losing staff is climbing along with it. The threat is maximized by the lack of feedback and communication tools, a geographically isolated employee base, and the detachment from management.
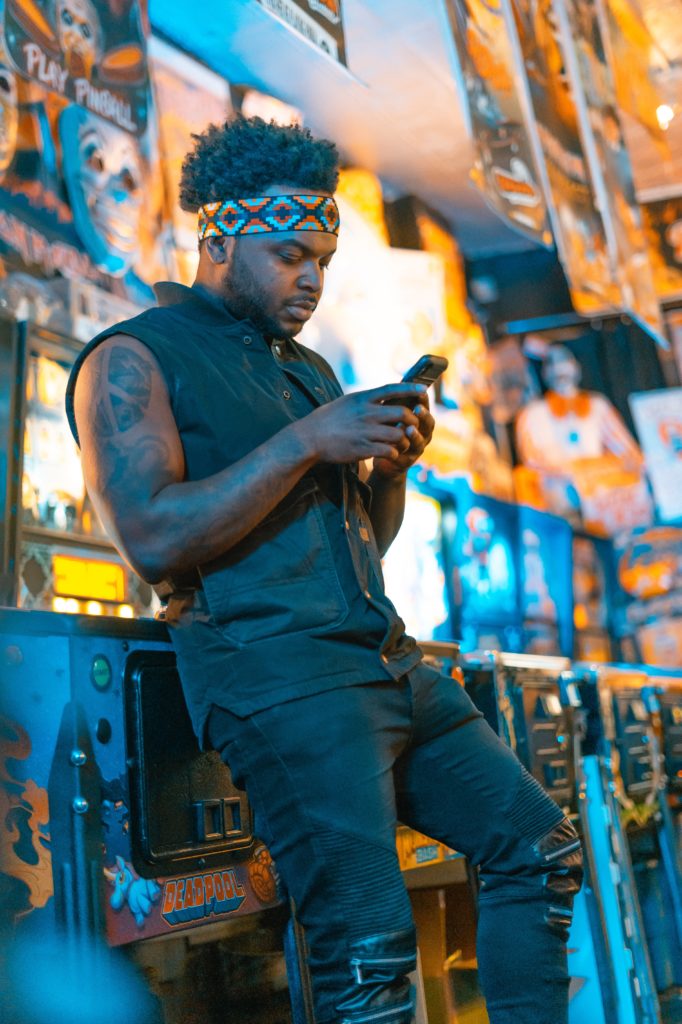
Bridging these gaps means creating an environment that increases productivity and inspires the commitment of every employee. To boost engagement, give your frontline staff the means to do their jobs efficiently. Integrating technology into manufacturing workplaces provides staff the tools to increase productivity and can streamline everyday processes to double efficiency.
Frontline Solution
In the manufacturing industry, frontline employees habitually struggle with inefficient communication methods, assigning and managing work orders and receiving pertinent information. This inability to access things when working on the line leads to frontline employee frustrations, miscommunications, and missed shifts.
There are many different software applications available to help with project management and scheduling tasks. An intranet can streamline operations and management by making it easy for managers to assign tasks, dispatch work orders, and manage the daily upkeep needed to exceed user expectations.
It’s simple to set up electronic forms, workflows and more, saving valuable employee time and improving accuracy and quality of information. Free your frontline team from the time you spend on recurring frustrations and inefficient team and organizational processes.
Training and development:
Manufacturing employs a higher share of workers without a college degree than the economy overall. As relevant as recruitment and poor engagement are to high turnover rates, training and development are just as vital.
Developing your frontline staff is critical to productivity and creating higher levels of employee satisfaction. Your employees need to feel not only valued but also that they are being invested in by their employer. Providing adequate training serves to keep them current with developments in the industry as well as prepare them to journey further along with their organization.
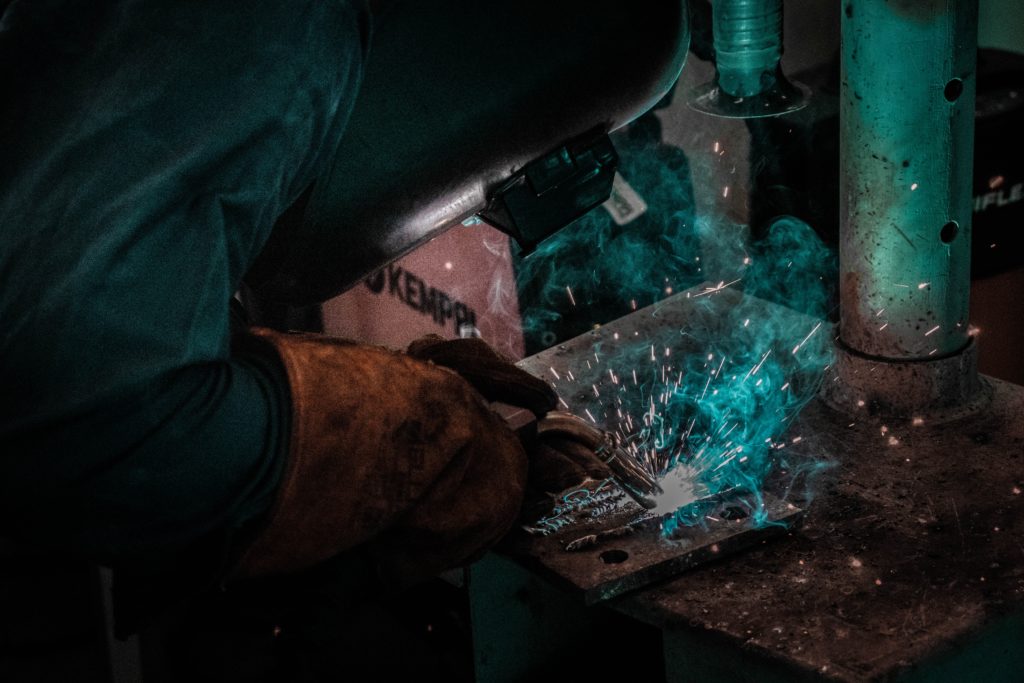
Luckily, 80% of manufacturers recognize the absolute importance of meeting workforce demands over the next five years.
Frontline Solution
Due to their
Online training programs and eLearning opportunities can be offered to employees looking to take their skills to the next level. Being virtual, programs allow staff to develop at their own pace while overcoming the everyday challenges of distance or timezone.
Manufacturing organizations can even try microlearning, a technique that condenses training into short bursts of learning activities that range from 2-15 minutes in length.
This way, employees can learn and advance from any location, as well as receive support from online users. Online and mobile development options are precisely what frontline staff needs: short, convenient, and easily accessible training.
Conclusion
Manufacturing companies are hampered with many obstacles to optimal employee engagement and productivity on the frontlines. Adopting a frontline-friendly strategy to workplace culture and employee satisfaction is the most effective way to address these challenges.
Implement the right digital and social tools in order to help your frontline employees grasp their full potential as the face of your organization.